Asset Tracking Platform: Tools, Equipment, Health & Safety
Cappagh Browne Utilities
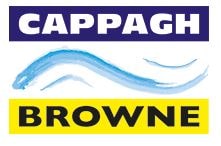
Cappagh Browne is a UK utilities company that specialises in repairing and maintaining Southern Water’s wastewater networks for 4.7 million customers across the South East of England. The company’s remote teams of engineers service more than 40,000km of wastewater pipes spanning from the New Forest to the Kent coast. Cappagh Browne approached Assettrac to deliver an asset tracking platform that would help them manage tools, equipment and health and safety for remote working teams.
To service this wide area, the company employs more than 500 people and has over 100 operational teams and their vehicles that need to be ready and equipped to respond to any incident wherever it is. In the 2022-23 period, the teams responded to over 60,000 call-outs.
In the UK water and waste sector around 8,000 workers sustain a work-related injury every year. Not only is this a worry for individual safety and wellbeing, it has a knock-on effect of lost working days and efficiency. Unsurprisingly, this means safety is a top priority and for Cappagh Browne, it is its guiding mantra.
How Tracking Assets Effectively Improves Safety & Costs
“One of the only things I lose sleep over is safety. I have people working all over the place and usually I don’t know if there is a specific problem until it’s reported to me. Using digital asset tracking gives me immense peace of mind because I can be sure we’re following the correct procedures and processes and that everyone has the equipment they need,” comments Managing Director, Jeff Birtwhistle.
Without careful management and an effective safety culture, the utilities sector can be a high risk working environment. Operating across a wide geographical area with more than 500 people split across over 100 remote teams, the business needed to ensure that all team members had all the safety and business critical equipment required to technically do the job as well as to minimise incidents.
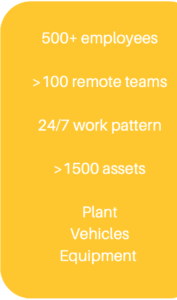
Typically, each team will carry a lot of equipment (both owned and hired) and the company needed a more effective way to track and manage each van’s equipment, inspection and maintenance cycles, losses, as well as equipment hired. Just one piece of missing equipment will affect a team’s safety and ability to do the job explains Birtwhistle,
“Whenever we dig holes, there are so many things down there that can kill us, like live electricity or high pressure gas or water. If you’re missing a cat and genny (which helps us identify the services below ground using radio waves) you won’t know where the underground services are and therefore can’t dig around them. It’s a mission critical piece of equipment that frankly, can get lost in so many ways. Sometimes the teams don’t even know it’s missing because they’ve put it down somewhere and missed it when they pack up.”
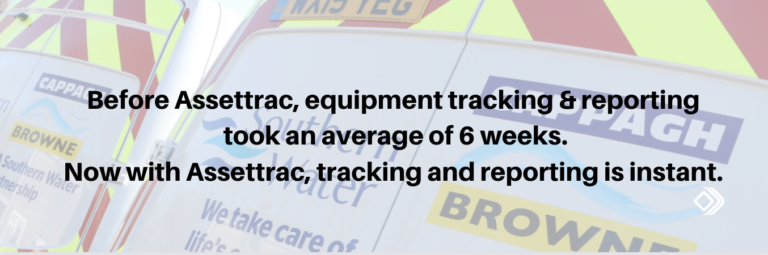
The manual audit paper train was slow – it could take 6 weeks to report on missing equipment. Operationally, teams work 24/7 and can be called out at any time. In order to optimise productivity, the management wanted engineers to be focusing on operational tasks rather than spending all their time logging equipment on paper audit sheets every week. At the same time, they needed to keep track of more than 1500 items including plant, equipment and vehicles.
The key problem was that the manual audit paper trail was slow. With teams working in the field it took a long time for the paper audit sheets to be received at head office and then processed by the admin team. Typically it could take 6 weeks to report on equipment, by which time the situation may have changed. There was never a clear view of what critical equipment was missing and this meant there was an increased accident risk because operatives didn’t have the equipment they needed to keep them safe.
Asset Tracking Platform for Managing Tool & Equipment Assets in the Field
Cappagh Browne’s customised digital asset tracking portal enables them to audit all equipment remotely every week, even if a remote-working team hasn’t come back to base. Any team member can evidence they have their equipment in their vehicle by tapping it against the item tags, either using their phone or a handheld device.
All scanned item data is instantly uploaded to the cloud meaning that the company no longer has to wait for paperwork to come into the office to know if any equipment is missing. The team at HQ can call to check if they have just forgotten to scan it, or whether it’s missing from their van. The solution can be immediate, as the team member can immediately scan the missing item’s asset tag if it is in the vehicle..
As a result, Cappagh Browne can now keep an accurate record of which equipment is out in the field and what servicing or replacement is required, giving them the confidence that teams can do their jobs efficiently and in the safest way possible.
Instant Reporting: Asset Tracking Reports Produced 6 Weeks Faster
Following the launch of their customised cloud asset tracking system and tagging from Assettrac, Cappagh Browne saw a massive improvement in data visibility and speed of reporting. Under the manual paper audit system, it could take 6 weeks from an audit checklist being completed to having the reporting data, and now it’s instant. Operations can now run a quick weekly report to check if anyone has missed the audit and to identify any missing items and can then take immediate action to make sure the team has the equipment they need
Additional Operational Benefits
Equipment Maintenance & Asset Lifecycles
Digital equipment audits enable the business to track maintenance, calibration and servicing requirements for all equipment. The information is stored centrally and reports 60 days in advance on what equipment needs to be inspected and serviced; even when vehicle tax needs to be updated. The system shows a history for every item, tracking its lifecycle from purchase order to decommission, waste or return of hired equipment.
Cost Savings for Equipment & Tool Assets
With an accurate register of all equipment, Cappagh Browne can more effectively manage their inventory. Accurate, up-to- the-minute visibility saves unnecessary costs on hired equipment and replacements. The company also benefits from cost and time savings in administration because of the increased speed of data collection and reporting.
Real-time Asset Reporting
By making tracking easier and less admin heavy for engineers, Cappagh Browne now has more asset data to work with and more detailed business intelligence. As data is instantly updated, reporting is more accurate and actionable. The customised portal was set up with automated reports that can be run at the click of a mouse and an interface with Google Looker (Data Studio) helps teams easily run their own bespoke reports.
Comprehensive Safety Audits
Assettrac provides a robust mechanism to undertake safety audits and gives greater visibility than was ever achieved with a manual paper system.
A Customised Asset Tracking Platform in just 60 Days
As SaaS software has developed over the past 20 years, the ability to configure software uniquely to a business needs has become much easier. Previously, customised software was out of reach for many organisations due to cost and time to implementation.
Jeff Birtwhistle comments;
“There are various suppliers who can deliver an asset tracking solution but they are not all cut from the same cloth. We were quite a long way down the road of testing and scoping suppliers but we were meeting obstacles with time to implementation, on-going management and future development costs. Then we came across Assettrac. They were simply more agile. Assettrac could do everything we wanted and fast. Importantly, it also gave us the opportunity to develop the system over time without high on-going financial costs.”
For Cappagh Browne, the first scoping meeting to the implementation of their custom portal and training was a matter of weeks. The only challenge for the business was the speed with which they were able to tag their equipment with their custom NFC tags due to teams working remotely. Once tagged, the process has been easy to implement.
Initial training was provided by Assettrac and the company has provided further tagging and reporting training in- house. “It’s quite intuitive to use. The training has been excellent,” comments HQ Manager, Aves Bellamy. “The system has really made a difference to the way that I work. It gives you confidence that you’ve got all the right information at your fingertips.”
A Return-on-Investment Greater than Pounds & Pence
Jeff Birtwhistle continues;
“It’s become an integral tool in our business. In terms of return on investment, actually the value is more than pounds and pence. It’s more in governance and control, giving visibility of the actual facts on systems and controls helping us ensure we meet our legal requirements.
“Our industry is not without its accidents and incidents. This year we expect to do more than 66,000 jobs and safety is probably the only thing in my job that unnerves me. There are massive implications with safety out there.
It’s a return on investment in terms of sanity, of knowing that we’ve got the level of governance and control that we need. Not only can we use that governance and control to make sure we’re doing the job right, but then we can evidence what we’ve done so from time to time when something does go wrong, we can show that we’ve got the systems and processes in place.”
Read the full white paper by downloading it here.